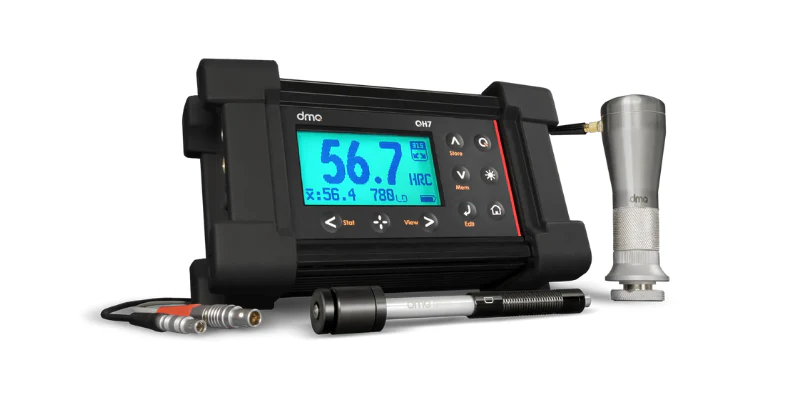
How to Choose the Best Hardness Tester for Your Industry?
Introduction: The Importance of Hardness Testing in Modern Industries
In industries where material strength and durability are critical, hardness testing plays a key role in ensuring product reliability. Whether it's aerospace components, automotive parts, or construction materials, understanding material hardness helps manufacturers maintain quality and compliance with industry standards.
This guide will take you through what hardness testers are, their types, working principles, and how to choose the best hardness tester for your needs.
What is a Hardness Tester and How Does it Work?
A hardness tester is a device used to measure a material’s resistance to indentation, deformation, or scratching. It applies a specific load via an indenter and measures the resulting penetration depth or material response.
Key Components of a Hardness Tester:
- Indenter: A ball, cone, or diamond point that applies force to the material.
- Load Mechanism: Controls the amount of force applied.
- Measuring System: Records indentation depth or other hardness values.
- Display Unit: Shows the hardness reading based on the test performed.
Why Hardness Testing is Essential?
- Ensures Durability: Harder materials resist wear and tear, ensuring longer lifespans.
- Quality Control: Helps manufacturers verify material properties before mass production.
- Material Selection: Ensures the right materials are used for specific applications.
- Compliance with Standards: Confirms materials meet industry benchmarks like ASTM, ISO, and IEC.
Types of Hardness Testers and Their Applications
Hardness testers come in various types, each suited for different materials and industries. Let’s explore the most widely used hardness testing methods.
1. Ultrasonic Contact Impedance (UCI) Hardness Tester
- Uses ultrasonic vibrations to measure hardness.
- Ideal for thin materials, coatings, and heat-treated surfaces.
- Provides quick, non-destructive hardness testing in field applications.
2. Combined UCI and Leeb Hardness Tester
- Integrates both UCI and Leeb testing methods for comprehensive analysis.
- Suitable for varied material types including metals, coatings, and industrial parts.
- Provides accurate and fast hardness measurements across multiple applications.
- Used in field inspections, quality control, and industrial testing.
3. Brinell Hardness Tester (BHN)
- Uses a steel or tungsten carbide ball as the indenter.
- Suitable for testing coarse materials like cast iron, aluminum, and non-ferrous metals.
- Measures the diameter of indentation under a heavy load.
4. Rockwell Hardness Tester (HRB, HRC, etc.)
- Uses steel or diamond cone indenters.
- Measures depth of indentation, making it faster than Brinell testing.
- Commonly used in metalworking, automotive, and aerospace industries.
5. Vickers Hardness Tester (VHN)
- Uses a diamond pyramid-shaped indenter.
- Provides highly precise measurements for microhardness testing.
- Ideal for thin materials, coatings, and small parts.
6. Knoop Hardness Tester (KHN)
- Used for extremely thin materials, coatings, and surface layers.
- Measures indentation using a narrow diamond tip.
7. Mohs Hardness Test
- Measures scratch resistance of minerals and materials.
- Uses a scale of 1 (talc) to 10 (diamond).
- Commonly used in geology and gemology.
8. Rebound (Leeb) Hardness Tester
- Measures elastic rebound of a test probe.
- Portable and ideal for large, heavy industrial components.
Choosing the Best Hardness Tester for Your Needs
To select the best hardness tester, consider the following:
- Material Type: Are you testing metals, plastics, ceramics, or coatings?
- Required Accuracy: Do you need macro or microhardness testing?
- Portability Needs: Is a stationary or handheld tester more suitable?
- Industry Standards: Does it comply with ASTM, ISO, or IEC standards?
Key Industrial Applications of Hardness Testers
1. Aerospace Industry
- Ensures high-strength alloys used in aircraft withstand stress.
- Verifies materials in engine components and landing gear.
2. Automotive Industry
- Tests brake pads, gears, and crankshafts for wear resistance.
- Ensures safety and performance of structural components.
3. Manufacturing & Quality Control
- Monitors steel, aluminum, and polymer materials for consistency.
- Helps prevent premature material failures in industrial production.
4. Medical Implants & Devices
- Tests biomedical materials like titanium, ceramics, and alloys.
- Ensures medical implants meet safety and durability standards.
5. Construction & Civil Engineering
- Measures concrete and steel hardness for building infrastructure.
- Helps engineers select suitable materials for extreme environments.
Common Hardness Testing Challenges & Solutions
1. Environmental Factors
- Issue: Temperature fluctuations affect test accuracy.
- Solution: Conduct tests in a controlled environment.
2. Operator Errors
- Issue: Incorrect force application leads to inconsistent results.
- Solution: Use automated or digital hardness testers.
3. Calibration Issues
- Issue: Machines lose accuracy over time.
- Solution: Perform regular calibration checks using standard reference blocks.
Maintaining and Calibrating Your Hardness Tester
- Routine Maintenance: Clean the device to remove dust and debris.
- Calibration Checks: Use certified hardness blocks for verification.
- Inspection & Upgrades: Replace worn-out indenters and update software.
Future Trends & Innovations in Hardness Testing
- Digital & Automated Testers: Improve precision and efficiency.
- Non-Destructive Testing (NDT): Allows testing without damaging materials.
- AI & Data Analytics: Uses machine learning to predict material behavior.
How Often Should Hardness Tests Be Conducted?
- For high-stress applications: Frequent testing is required.
- Routine quality checks: Scheduled according to industry regulations.
- Research & Development: Regular testing ensures material advancements.
Ensuring Compliance with Industry Standards
Key International Standards for Hardness Testing:
- ASTM E18: Rockwell Hardness Testing.
- ISO 6506: Brinell Hardness Testing.
- ISO 6507: Vickers Hardness Testing.
- ISO 6508: Rockwell Hardness Testing.
Final Thoughts: Why Hardness Testing is Indispensable
Hardness testers play a vital role in industries worldwide, ensuring material strength, durability, and compliance with international standards. As technology evolves, digital and automated solutions continue to improve the precision and efficiency of hardness testing.
FAQs
1. Which hardness testing method is the most accurate?
Vickers and Knoop hardness tests provide the highest precision for microhardness testing.
2. How frequently should a hardness tester be calibrated?
At least once a year, or as per industry regulations.
3. Can hardness testers be used on all materials?
Different testers suit different materials; Rockwell is best for metals, while Mohs is used for minerals.
4. What causes errors in hardness testing?
Errors arise due to misalignment, improper force application, and environmental factors.
5. How does temperature impact hardness testing?
Higher temperatures soften materials, while colder temperatures may make them brittle.
Leave a comment